Why Cleanroom Manufacturing is Essential for Medical Adhesive Tapes and Films
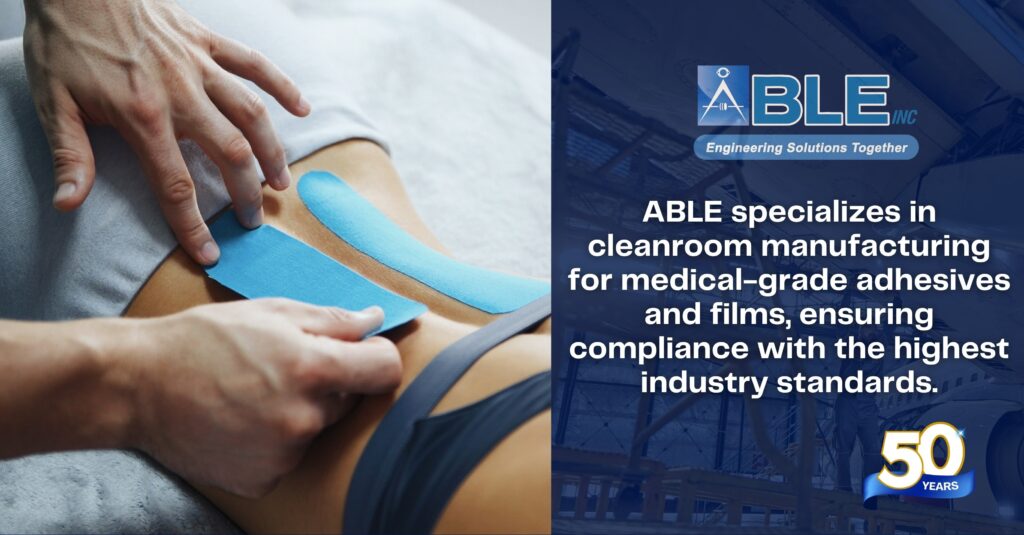
Medical adhesives are widely used as wound care products, in surgical operations, and in the manufacture of wearable medical devices. Cleanroom manufacturing ensures that these items are free from contamination by dust, moisture, or microorganisms, guaranteeing product quality and patient safety. This controlled environment is important to maintain the right adhesion strength and prevent the formation of bad bacteria or mold.
The Importance of Adhesive Tapes and Films in Medical Devices
Medical adhesive tapes and films are essential components in healthcare, offering versatile solutions across various applications:
- Wound Care: These adhesives secure bandages and dressings, protect wounds from external contaminants, and promote healing by holding the skin together. Transparent films also allow medical staff to monitor wounds without frequent dressing changes, reducing the risk of infection.
- Surgical Tapes: During surgeries, adhesive tapes secure incisions, drapes, and medical instruments in place. They ensure that tubing and catheters remain attached to the body, preventing accidental dislodgement and ensuring smooth operations.
- Diagnostics and Wearables: Adhesives play a key role in attaching sensors, electrodes, and transdermal patches to the body in diagnostic devices. These tapes provide a stable connection for devices monitoring heart rate, glucose levels, or brain activity, ensuring reliable data collection.
- Medical Tubing and Prosthetics: Adhesive films help anchor IV lines, catheters, and prosthetics, improving patient comfort and preventing accidental disconnections or irritations.
Medical adhesive tapes and films enhance the security of patients through a painless fixation process without any risk of skin sensitivity through the use of skin-friendly and breathable materials. They keep clean to minimize contact with diseases that may occur during treatment or the healing process. These adhesives also improve the utilitarian function of a device through secure positioning, precise tracking, correct dosing, and protection from moisture and fluids, in worst-case scenarios as well.
What is Cleanroom Manufacturing?
Cleanroom manufacturing entails the fabrication of products in a chamber whose airflow, temperature, and relative humidity are controlled in a manner that reduces contamination from dust, microbes, or any debris floating in the air. HEPA filters are used to guarantee cleanness, which is expressed in particle counts per a given volume, for example, ISO 6 or ISO 7. When it comes to medical-grade products, any contamination from particles, moisture, or dust can have great effects on the product’s quality and the patient’s health.
Contamination Risks in Medical Adhesive Tape and Film Manufacturing
Potential sources of contamination that affect the manufacturing of medical adhesive tapes and films are dust, bacteria, mold spores, and moisture since all affect both adhesion and sterility. These trace contaminants can reduce adhesion and cause product failure in high-stakes uses such as wound management, surgery, and diagnostic testing. Contamination has a high likelihood of causing infections and complications to users, particularly in cases where they have wounds or invasive devices. In addition, due to the weak adhesive, devices such as sensors or patches may come off leading to false readings or poor treatment outcomes.
How Cleanroom Manufacturing Prevents Contamination
Cleanrooms are designed to minimize contamination threat thus maximizing product quality, particularly in health manufacturing. Several key elements contribute to this controlled environment:
- Filtration: HEPA (High-Efficiency Particulate Air) filters that manage to remove particles with a size of no more than 0.3 microns. These filters remain to provide permanent air purification service as they eliminate dust, allergens, bacteria, and any other particles in the air stream.
- Airflow: Another important element of cleanliness is control of the flow of air in the cleanroom since only restricted areas are fitted with unidirectional airflow systems that provide a consistent flow of filtered air over the working area.
- Personnel Protocols: Sanctioned operation conditions are strongly associated with strict rules of gowning control for the personnel, including cleanroom suits with gloves, hats, masks, and shoe covers. Training is useful to eliminate contamination threats since personnel understand proper handling procedures when performing functions.
Quality Assurance in Cleanroom Manufacturing
It is crucial to maintain cleanroom manufacturing practices that meet the standards within its field in order to improve the quality of the product, as well as, prevent contaminants which are crucial to the safety of medical-grade products. This compliance provides customer satisfaction and shows concern towards regulatory standards in overall manufacturing effectiveness.
ABLE’s ISO certifications relevant to cleanroom manufacturing:
ISO-6 Certification (Class 1,000 Cleanroom)
Maintains air cleanliness with no more than 1,000 particles per cubic foot.
Incorporates HEPA filtration systems to ensure minimal airborne contaminants during fabrication and assembly processes.
ISO-7 Certification (Class 10,000 Cleanroom)
Ensures air cleanliness with no more than 10,000 particles per cubic foot.
Supports processes such as precision cutting and assembly while maintaining a contaminant-free environment.
Why Cleanroom Manufacturing is Crucial for Medical Adhesive Tapes and Films
Medical adhesive tapes and films must be manufactured under very clean conditions for reasons of safety and reliability since contamination will seriously affect the adhesion and sterility of the product. For example, adhesive products manufactured in controlled cleanroom environments achieve lower, more acceptable, microbial growth levels and better maintain material purity resulting in better medical applications than products manufactured in an environment contaminated with dust, fog, and other particles that affect adhesion or sterility.
Choosing ABLE for Cleanroom Manufacturing
ABLE boasts extensive expertise in cleanroom manufacturing specifically tailored for medical-grade adhesives and films, ensuring adherence to the highest industry standards. Our commitment to quality, precision, and safety is evident in every step of our cleanroom facility services, guaranteeing products that meet stringent regulatory requirements. With state-of-the-art facilities and ISO-certified cleanrooms, ABLE delivers exceptional solutions that enhance patient care and device functionality.
Cleanroom manufacturing is essential to the safety, quality, and performance of medical adhesive tapes and films mainly because it averts contamination hazards that are destructive to products. When trusting ABLE with cleanroom capabilities, you receive advice and services provided by a team with vast experience, following industry regulations and best practices, focused not only on product quality but also on improving the patients’ lives and the effectiveness of the devices being produced.
Choose ABLE for top-quality cleanroom manufacturing of medical adhesive tapes and films!
References:
https://www.linkedin.com/pulse/understanding-cleanroom-classifications-iso-8-7-6-5-charles-lipeles
https://able123converting.com/capabilities/clean-fabrication-facilities/