Custom Converting Solutions for Electronics: Precision Materials for Performance & Reliability
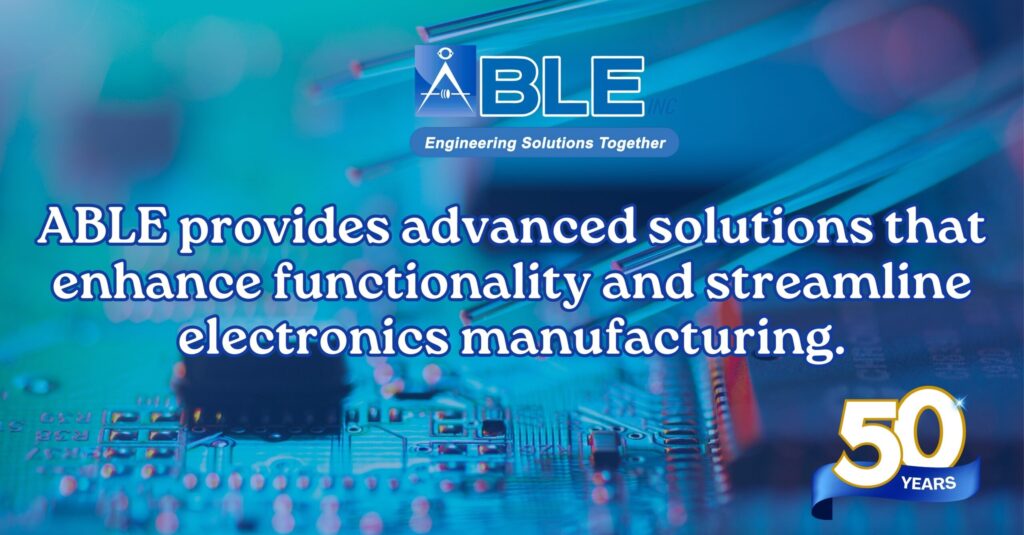
Custom converting is a fundamental process that has revolutionized the electronics industry by enabling the precise shaping, cutting, and laminating of advanced materials. These solutions enhance the performance and functionality of electronic components, ensuring reliability in high-tech applications. Custom-converted materials are essential in optimizing efficiency and durability, from thermal management and EMI shielding to adhesive bonding and insulation.
What Are Custom Converted Solutions for Electronics?
Custom converting involves modifying raw materials into specific shapes, sizes, and designs to meet the needs of various industries, including electronics, medical, automotive, aerospace, and renewable energy. These solutions ensure that materials are precisely engineered for their intended applications, improving performance, durability, and efficiency.
In the electronic industry, for example, custom converting plays an essential role in thermal management, electrical insulation, EMI shielding, and gasket solutions. By using advanced techniques manufacturers can seamlessly integrate high-performance materials into their products.
Techniques used in custom converting:
- Die-Cutting: Creates precise shapes for gaskets, insulation, and protective covers.
- Laminating: Bonds layers for added strength, durability, and protection.
- Slitting & Precision Cutting: Cuts materials to exact sizes for easy assembly.
- Printing & Coating: Adds markings, coatings, or branding for functionality.
Benefits of Custom Converting in the Electronics Industry
Precision and Consistency
- Advanced cutting and slitting methods ensure that materials fit precisely into electronic assemblies.
- High consistent quality is less waste and better production efficiency also carries.
Improved Performance and Reliability
- Specialized thermal management solutions, e.g. heat dissipating films and thermal interface materials increase the lifespan of electronic devices.
- EMI shielding materials shield sensitive parts from electromagnetic interference thereby maintaining the function stable.
Enhanced Efficiency in Manufacturing
- Pre-cut and pre-crafted components decrease the time to assemble and reduce costs.
- Adhesive-backed and die-cut components reduce the manufacturing process by eliminating the need for post-processing.
Versatility Across Applications
- Custom gaskets and seals prevent dust, moisture, and contaminants from affecting electronic devices.
- Specialty tapes and bonding solutions provide strong, durable adhesion for complex assemblies.
Custom Solutions for Electronic Applications
1. Thermal Management Solutions
Overheating can cause damage to the electronic parts, making efficient heat dissipation essential. Custom thermal management materials help in maintaining temperature and in increasing device reliability.
- Thermal Interface Materials (TIMs): Pre-cut thermal pads and gap fillers, as well as conductive tapes, enhance heat removal.
- Heat Spreading Films: Graphite or phase-change custom-cut materials provide even heat distribution across surfaces.
- Insulating Barriers: Insulating barriers made from polyimide or silicone have been die-cut to shield and shield electronics from heat stress.
2. EMI/RFI Shielding Solutions
Electromagnetic interference (EMI) and radio-frequency interference (RFI) can interrupt electronic signals causing malfunctions or even reducing performance. Custom shielding solutions protect sensitive components from unwanted interference.
- Conductive Tapes and Films: Custom-cut shielding tapes with conductive adhesives provide seamless EMI protection.
- Foil Laminates: Cut-to-size copper or aluminum foils block the undesired electromagnetic waves.
- Shielding Gaskets: Conductive-coated foam or rubber gaskets gives an air-tight EMI.
3. Electrical Insulation Solutions
Preventing short circuits and electrical failures is critical for device safety and functionality. Custom insulation materials provide protective barriers between conductive elements.
- Dielectric Films: Polyimide, polyester, or PTFE films provide excellent electrical insulation.
- Custom-Cut Tapes: Pressure-sensitive adhesive tapes insulate components while allowing easy application.
- Gaskets and Seals: Silicone, rubber, or foam materials prevent moisture and dust from affecting circuitry.
4. Bonding and Adhesive Solutions
Secure attachment of electronic components is necessary for long-term durability and structural integrity. Custom bonding solutions simplify assembly while ensuring strong adhesion.
- Adhesive Transfer Tapes: Custom die-cut tape bond components without adding bulk.
- Structural Adhesives: High-strength adhesives provide long-term durability in demanding applications.
- Repositionable Adhesives: Allow for easy component adjustment during assembly.
5. Gasketing and Sealing Solutions
Electronic systems operating in hostile surroundings need to be shielded against dust, water, and chemicals. Custom gaskets and seals also prevent abuse and damage to the units.
- Custom-cut foam Gaskets: Accessories to enclose to keep dust, moisture, and chemicals out.
- Liquid Gaskets and Form-in-Place Seals: Provide flexible sealing for intricate designs.
6. Acoustic and Vibration Damping Solutions
Excessive noise and vibrations can lead to mechanical failures and decreased product longevity. Custom damping materials reduce unwanted sound and mechanical stress.
- Vibration Damping Foams: Absorb shocks and reduce mechanical stress on components.
- Sound Absorbing Materials: Custom-cut foams or fabrics minimize unwanted noise in consumer electronics.
Partnering with ABLE Custom Converting Solutions
Selecting the correct partner for custom converting solutions is very important to achieving the accurate, precision-engineered materials necessary for electronic applications. Over 50 years of expertise have allowed ABLE to develop cutting-edge precision slitting, die-cutting, laminating, and other advanced material conversion techniques that meet the most demanding specifications in the industry. ABLE’s leading-edge technology and expertise in the fields of technology and engineering allows us to use high-performance materials to obtain the optimal functionality, durability, and efficiency in the electronic components. Together with ABLE, manufacturers receive a long-term trusted partner which brings new, cost-efficient, and high-quality solutions to enable performance increase and production streamlining.
Custom conversion solutions are essential in maintaining precise, dependable, and efficient operation of electronic manufacturing. From thermal management and EMI shielding to insulation and bonding, these customized solutions improve device performance and reliability. By applying cutting-edge material processing technology, manufacturers can improve manufacturing efficiency, decrease waste, and achieve the best performance of the products.
Partner with ABLE today to elevate your electronic components with precision and expertise.
References:
https://blog.marianinc.com/blog/electronic-applications
https://able123converting.com/materials/
https://www.rbbsystems.com/blog/tailoring-solutions-the-benefits-of-custom-electronics-manufacturing
https://able123converting.com/applications/
https://able123converting.com/blog/able-industrial-converting-solutions-driving-success-across-industries/