ABLE Inc.: Impeccable Converting Capabilities
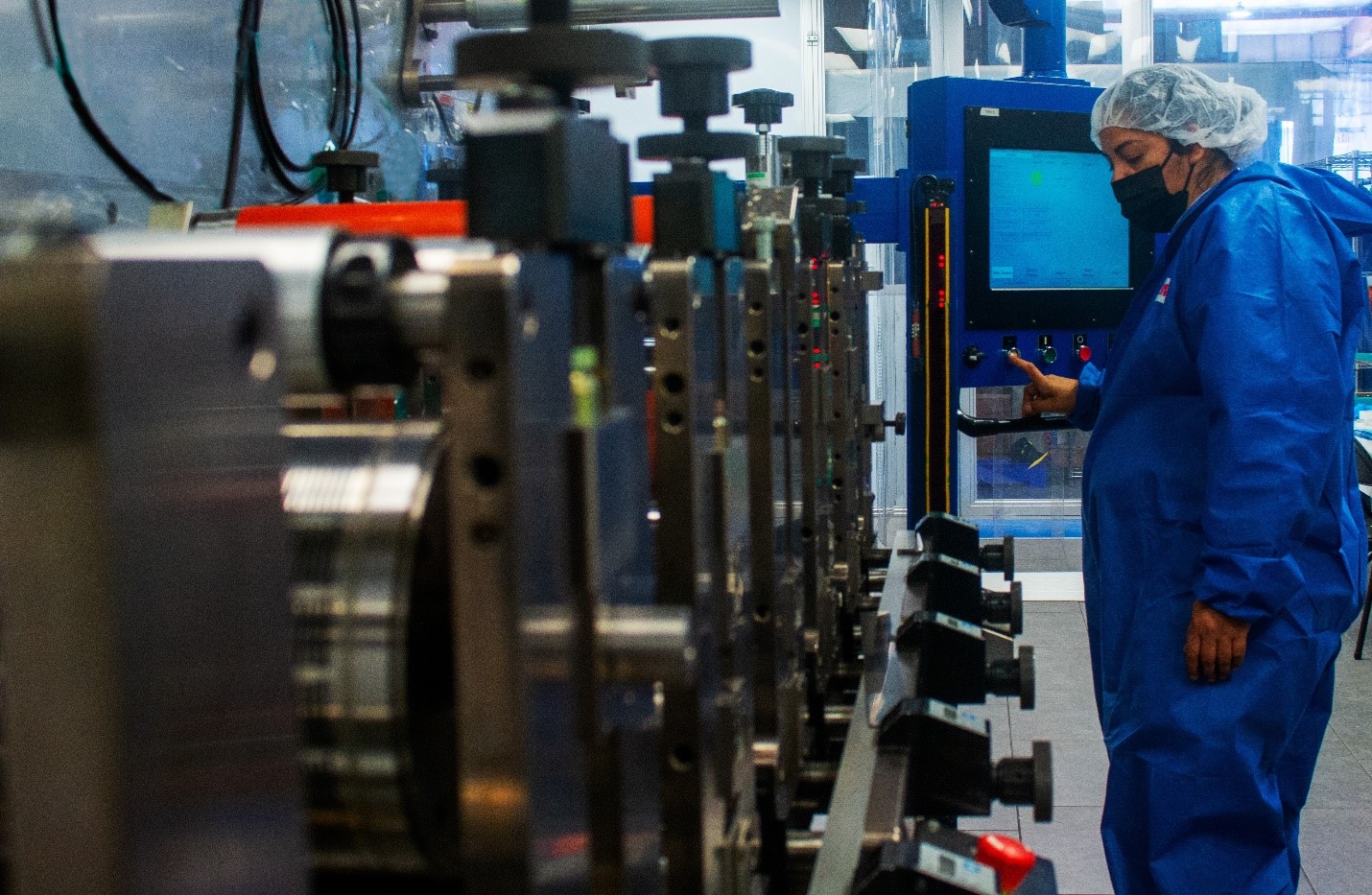
One of the many benefits of working with a custom converter is tapping into your partner’s converting capabilities and material expertise. Through effective consultation and collaboration, a converting company is able to help you determine the ideal materials and converting solutions for your specific needs and applications. When outsourcing converting solutions, the primary goal is to enhance product quality, streamline your manufacturing process, and cut costs. In order to accomplish those objectives, partnering with a trusted converter like ABLE and establishing a collaborative process are the ultimate keys to developing a custom converting solution.
ABLE Inc.: Impeccable Converting Capabilities
While the possibilities with converting are virtually endless, ABLE Inc. provides impeccable converting capabilities suitable for various industries. Listed below are ABLE’s 12 impeccable converting capabilities:
Custom Die Cutting
In the converting contractor industry, die cutting is a fabrication process that involves cutting shapes from materials including adhesives, films, foams, and rubbers. ABLE rotary die cutting can create almost any shape from any custom material, ranging from film to converted materials including adhesive-backed foam. It is also optimal for items that require a tight tolerance and high-volume orders requiring a tight turnaround.
Laser Cutting
Laser cutting is used in place of a custom metal die or metal blades, using heat from laser light to cut into the converting material. ABLE can help our client achieve the right shape, dimension, and the right size through software programmed into a computer that guides the movement of the beam.
Water-jet Cutting
In a custom converter setup, water-jet cutting carries a narrow, pressurized stream of water to cut the shape from the material. An abrasive material is sometimes added to the water solution, especially when working with harder materials or thick, heat-resistant foams. ABLE’s water-jet cutting can slice through just about any material, especially those that are difficult to cut including thicker foams and heat-resistant materials, like silicone.
Rapid Prototyping
Crafting a die-cut prototype is a crucial final step in the design process. A prototype of a custom converted part offers a high-fidelity representation of the finished part, made to exact dimensions and specifications. ABLE’s rapid prototyping program is one of the best converting solutions and helps our clients meet their production deadlines.
Clean Fabrication Facilities
In any industry, cleanroom facilities are certified to keep the workspace clean and dry, so that adhesive and packaging are free of dust, particles, mold, and moisture. ABLE Inc. has the cleanroom manufacturing environment to help our clients meet their requirements from start to finish: assembly, fabrication, and packaging.
Router Knife Cutting
Router knife cutting offers blade-cut shapes out of foams, foils, paper, and other materials at a high level of precision. ABLE’s Zünd G3 flatbed cutter comes with multiple tool components and settings to achieve near-perfect cuts on any material using the perfect blade.
Lathe Slitting & Spooling
In the converting industry, lathe slitting is the most common method used to develop a custom-sized roll of tape. When a client needs a pressure-sensitive adhesive in a custom width, and it’s not available from the manufacturer, ABLE’s lathe slitting provides a cost-effective solution.
Custom Laminating
Laminating is an important part of the converting process. Whether our client’s converter is meant to hold a filter in place, create insulation in electronics, or provide protection against moisture and particulates, ABLE’s technical experts can boost the functionality of the overall product.
Horizontal Foam Cutting
Every foam converter project begins by obtaining the foam material at the precise thickness. Whether a design calls for an insulating shield for an electronic device or a die-cut foam gasket, ABLE can create a custom-sized foam sheet before you cut out the part. ABLE’s horizontal foam cutting can take our custom converting capabilities to a new dimension.
Custom Printed Tapes
ABLE’s three-color flexographic printing capabilities can enhance the look of a product. We custom print 3M™ tape on various web widths and lengths and precision cut to create just about any label. We can also custom cut the printed tape to meet various industries’ specific needs. ABLE can create a label on a roll, peel and stick removable instructions or just add a unique design element.
3D Printing
3D printing provides a quick, cost-effective solution for the test samples and proof of concept to move a project to production. With ABLE’s 3D printing, we can have the prototype on its way within 48 hours of receipt. ABLE’s 3D printing is part of our lineup of in-house rapid prototyping services.
Assembly & Kitting
When a custom converting project entails multiple parts, ABLE can package these into assembly and component kits. These eliminate the need to sort, compile and sequence disparate pieces, streamlining the preproduction process.
Partnering with an experienced custom converter will not only allow you to take advantage of these converting capabilities but also combine them with different materials to improve the design and performance of your product.
Do you want to try our converting capabilities? Hurry! ABLE is here to help you with your converting needs. Talk to us now!