Precision Slitting for Battery Production: Optimizing Materials for Energy Storage
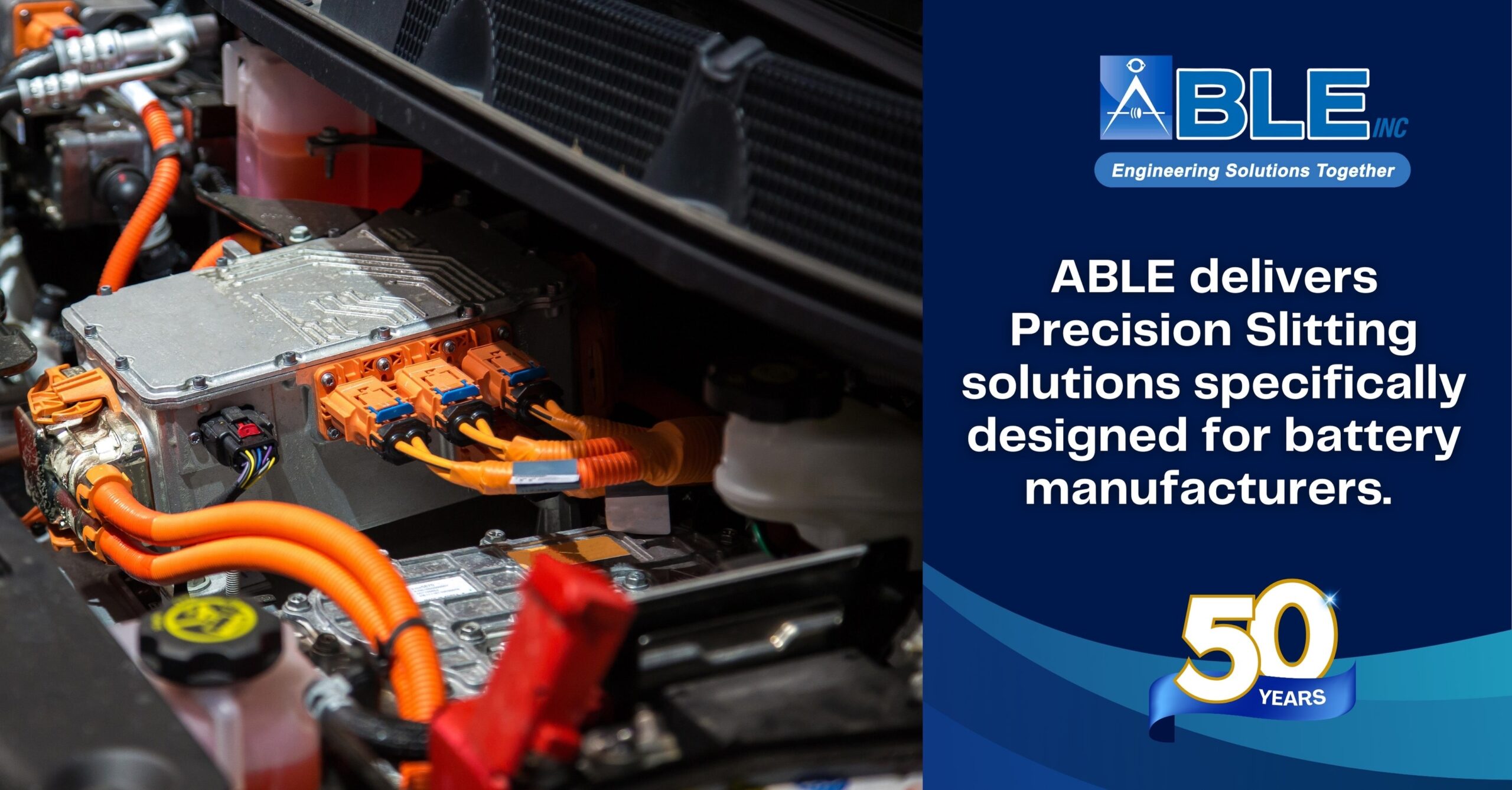
Precision slitting is an important contributing factor in the assembly of batteries. Over the years, there has been significant uptake of battery energy storage in electric vehicles, electronics, and other appliances, making it essential to improve the efficiency and quality of batteries in today’s market. Precision slitting technology is appropriate for achieving modern batteries’ intended level of thin ingredients.
Understanding Precision Slitting in Battery Manufacturing
Precision slitting on the other hand involves trimming large rolls of material into fine narrow tapes with specific thickness by employing advanced equipment and mechanisms, which are important for battery making, especially the electrodes or separators. This technique provides for uniform writing on width and quality, contributing to the uniformity of cell performance and cell safety. This means that accurate slitting is directly proportional to the efficiency and quality of the final battery cell because errors may result in unbalanced electrochemical reactions and failures affecting battery performance.
Key Materials in Battery Production that Uses Precision Slitting
Electrode Materials
In batteries, electrodes are elements that enable the chemistries required to store and release energy within the battery. These materials have to be well slit so that they have an accurate thickness for efficient functioning for the battery and precise slitting is achieved.
- Anode Materials: These materials must be slitted with high accuracy to ensure they fit perfectly within the battery cell and achieve optimal energy storage and release.
- Cathode Materials: Precision slitting of these materials ensures consistent thickness and uniformity, critical for maintaining the battery’s performance and safety.
Aluminum and Copper Foils
This is because aluminum and copper foils serve the purpose of current collectors in battery electrodes to transport electrical current through the material layers. Thinner copper foils applied on the anode side should be slitted to bear the load as required without adding extra resistance or causing overheating. Similarly, aluminum foils used on the cathode side need to be cut accurately in terms of size to ensure their conductivity, and they should not delaminate or have poor contact points.
Separator Films
The separator films are very thin, electrically insulating films that keep the anode and the cathode apart to reduce instances of short-circuiting while at the same time allowing ions to flow. Common materials include polyethylene or polypropylene and they have to be slitted perfectly for the right thickness and size because if they are not, they may cause safety or performance problems. Precision slitting also helps to maintain the strength and integrity of the films against temperature fluctuations and other environmental conditions during the battery’s use.
Optimization of Material Usage Through Precision Slitting
- Reducing Waste: Precision slitting technology produces accurate cuts that minimize waste by ensuring consistent strip widths and optimizing slitting patterns. This approach lowers material costs and supports sustainability by reducing scrap from expensive, thin materials.
- Consistency and Thickness Control: It ensures uniform thickness of electrode materials and separator films, which is crucial for the even distribution of active materials. This consistency improves energy density and efficiency, avoiding performance issues caused by thickness variations.
- Improving Battery Performance and Longevity: It enhances battery quality by ensuring accurate layering of materials, which reduces resistance and improves energy transfer. Clean, precise cuts contribute to better overall battery performance and longevity.
Benefits of Precision Slitting in the Energy Storage Industry
- Improved Efficiency: Precision slitting cuts electrode materials to exact specifications, reducing waste and optimizing the use of costly materials like copper and aluminum foils. This accuracy helps maintain uniform thickness and width, enhancing the energy density and performance of storage systems.
- Enhanced Performance: Uniformly slit electrode materials ensure consistent electrochemical properties in each cell, improving battery performance and longevity. Precision slitting reduces internal resistance by maintaining correct alignment and contact of electrode materials.
- Cost Efficiency: By reducing waste and maximizing material use, precision slitting lowers the cost of materials for energy storage systems. Automation and high-speed slitting boost production rates and reduce labor costs, improving overall cost-effectiveness.
- Enhanced Production Scalability: Precision slitting systems support high-speed production lines, enabling manufacturers to scale up to meet the growing demand for energy storage solutions. Consistent slitting ensures each batch meets high standards, facilitating product quality and performance.
- Improved Battery Life: Consistent slitting ensures an even distribution of energy within the battery, extending cycle life and performance. Precision reduces issues like uneven wear or degradation of electrode materials, resulting in more durable and reliable storage systems.
- Customization: It allows for tailored electrode strips to fit specific designs and applications, supporting the development of specialized energy storage solutions for diverse needs.
Choosing ABLE’s Precision Slitting for Battery Production
Expertise in High-Tech Materials
ABLE demonstrates its expertise in high-tech materials for battery production through specialized knowledge, advanced equipment, and extensive experience. The company excels in handling materials like aluminum and copper foils, along with high-end separator films, ensuring precise management to maintain their performance. In terms of resolving the difficulties of battery materials slitting: preventing contamination, controlling material tension, and consistency issues – ABLE leverages advanced slitting technology and 50 years of experience.
ISO-Certified Quality Control
ABLE’s ISO 9001:2015 certification guarantees stringent quality management standards, ensuring consistent and reliable precision slitting. Additionally, their ISO 45001:2018 and ISO 14001:2015 certifications demonstrate a commitment to safety and environmental responsibility, further enhancing the quality of their services.
ABLE offers customized precision slitting services solutions to meet the specific needs of battery manufacturers, accommodating various material types and production requirements. ABLE’s approach allows for precise slitting dimensions and configurations, ensuring optimal performance for diverse battery applications.
The precision slitting process is very sensitive in the sense that electrode foils and separators have to be sliced properly to the required performances to avert any defaults. This improves battery durability and decreases waste from variability in essential features by cutting down on what this technology offers. The manufacturers can benefit from ABLE’s 50 years of expertise and slitting technologies to gain the most effective and efficient batteries.
Contact us to unlock the full potential of your battery production with ABLE’s precision slitting expertise!
References:
https://semcouniversity.com/laser-slitting-a-precise-but-pricey-option-for-battery-production/
https://www.hakusan.co.jp/english/products/slitter/da_mdl.html
https://www.nationalmaterial.com/what-is-precision-slitting/
https://able123converting.com/capabilities/precision-slitting/
https://able123converting.com/blog/quality-management-in-action-ables-certifications-and-commitment-to-excellence/