The Role of Custom Die Cutting in Medical Manufacturing
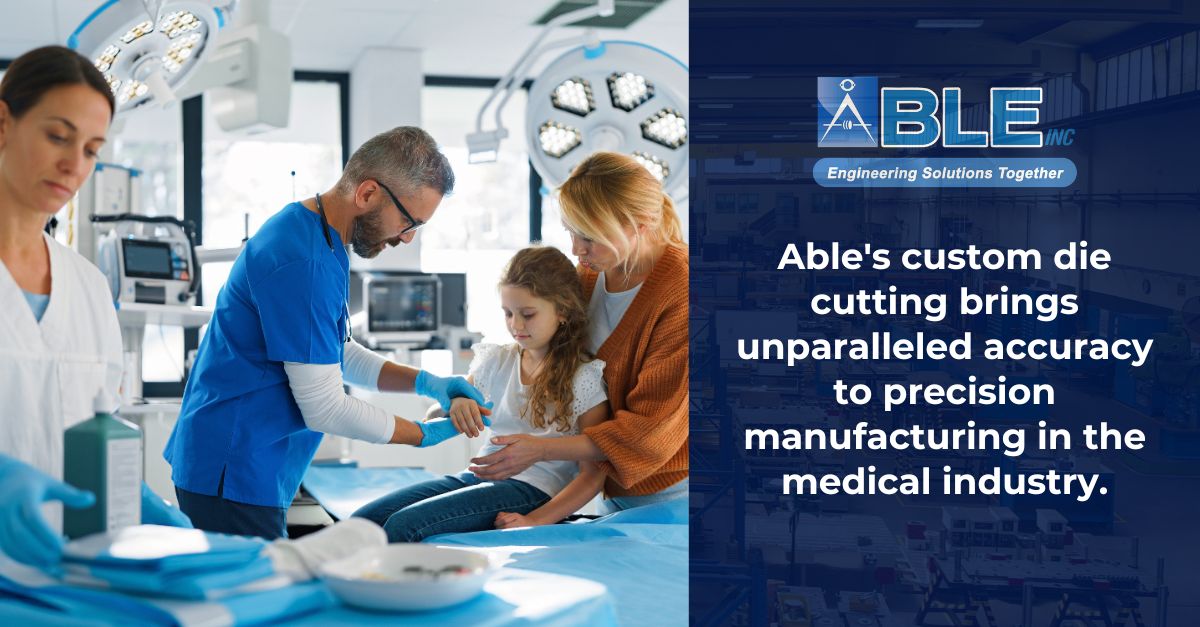
Custom die cutting involves accurately shaping various materials into specific forms using specialized tools to meet the requirements of diverse applications. This method is ideal for producing complex or delicate components, as it ensures that every cut is precise and consistent. In medical applications, precision is critical, as it guarantees the reliability and safety of medical equipment, which directly impacts patient care and treatment outcomes.
What is Custom Die Cutting?
Through the use of custom dies, materials are precisely shaped into various forms and designs according to individual demands. The fundamental concept is to shape various materials accurately and consistently using sharp blades or other cutting tools. Its converting capabilities make it ideal for producing complex and detailed components for a wide range of applications.
Types of Die-cutting
- Rotary Die Cutting: For high-speed, high-volume production, cylindrical dies are used in conjunction with a rotary press.
- Flatbed Die Cutting: Uses steel rule dies and a flatbed press to cut thicker or larger materials.
- Progressive Die Cutting: Makes continuous use of several stations inside a single die to create complicated forms.
- Laser Cutting: Uses a laser to achieve great precision and complicated designs without physical contact.
- Digital Cutting: Creates prototypes easily and quickly based on computer design using digital tools.
- Kiss Cutting: Good for stickers and labels because the top layer is cut away leaving the base intact.
- Through Cutting: Cut all layers separately.
- Perforating: Makes tiny holes or indentations that make tearing or separation simple.
- Creasing: Makes folding lines for precise folding of materials like cardboard and paper.
- Scoring: Makes folds without cutting for easier folding or bending
Importance of Custom Die Cutting in Medical Applications
Medical device performance and efficiency depend on the accurate and precise design of complex shapes, which is ensured by custom die-cutting converting capabilities. This position ensures that processes are executed with precision, in compliance with health regulations and standards, to ensure the safety and integrity of the patient. The reliability of medical equipment in the healthcare industry.
Materials Commonly Used in Die Cutting for Medical Purposes
- Adhesive tapes: Useful for fastening, sealing, and bonding tasks.
- Non-woven fabrics: Used in wearable medical devices and wound care items.
- Foams: Found in medical equipment for sealing, cushioning, and insulation.
- Plastics: The casings and disposable parts are made of polycarbonate, ABS, and polyethylene.
- Metals: Titanium and stainless steel for components that are resistant to corrosion and biocompatibility.
- Films: Used in medication delivery, filtration, and sensing applications.
- Composite Materials: Materials combined to provide biocompatibility, strength, and flexibility.
- Paper: Used for paper products such as labels and packaging inserts.
- Foils: Applied in packaging, decorating, and insulation purposes.
- Fabrics: Give wearable medical devices flexibility and comfort.
- Laminates: A combination of materials is used to give specific properties like strength and durability.
- Silicone: Often used in medical tubing and seals, silicone is biocompatible and flexible
Applications in the Medical Industry
Wearable Devices
Die-cutting is a crucial process in the production of wearable electronics which makes it possible to precisely shape flexible materials to fit various body types. This ensures that all components are snug and correctly aligned. Moreover, die-cutting makes it easier to create the exact electrode connections and adhesive patches needed for precise health tracking. Furthermore, expert die-cutting can offer smooth, comfortable materials that are gentle on the skin, enhancing comfort and adherence from the users.
Medical Packaging
Die-cutting is important in pharmaceutical packaging because it comes in different sizes and shapes to organize and protect pharmaceutical products. The use ensures that the goods remain clean and of high quality during transport. Sterilization pouches must be accurately and consistently sealed using die-cutting in order to retain their sterility until they are used. Ensuring the safety and security of medical devices and equipment requires security solutions.
Medical Device Manufacturing
Die cutting plays a vital role in the creation of medical devices, as it is responsible for making components that are both accurate and uniform. Die cutting creates essential parts such as gaskets, seals, and filters needed for the precision of diagnostic tools.
Benefits of Custom Die Cutting in Medical Applications
- High Precision and Accuracy: Custom die cutting ensures extremely precise and accurate shaping of materials, which is crucial for the functionality and reliability of medical devices.
- Material Efficiency: The process minimizes waste by optimizing material usage, making it an environmentally friendly and cost-efficient manufacturing method.
- Cost-Effectiveness: Die cutting is highly efficient, reducing production time and costs, which is particularly beneficial for large-scale manufacturing of medical components.
- Customization and Flexibility: Custom die cutting enables the fabrication of customized designs adapted to specific medical applications, giving the flexibility to satisfy various and specialized needs.
Setting Standards with ABLE’s Custom Die Cutting Services
ABLE’s custom die-cutting services emphasize rigorous quality assurance procedures and standards to ensure that each medical component meets the highest levels of precision and reliability. Technological advances, including digital and laser cutting, facilitate the creation of precise and complex shapes. ABLE stays at the forefront of material science innovations, incorporating new materials like biocompatible plastics and medical-grade foams. Our partnerships with companies such as 3M, Rogers Corp., and Sekisui Kasei provide access to high-quality materials needed for medical applications. Additionally, we embrace personalization and customization trends, offering tailored solutions that address the unique requirements of medical applications and equipment.
Custom die cutting is crucial for creating complex and detailed components due to its superior converting capabilities, precisely shaping materials using specialized tools. In medical applications, its precision is vital for ensuring device performance and safety, significantly influencing patient care and treatment outcomes. Advances in die-cutting technology and materials enable ABLE to provide high-quality, customized solutions that meet the evolving demands of the medical industry.
Contact us now to see how ABLE’s custom die cutting solutions can elevate the reliability of your medical products!
References:
https://www.americanmicroinc.com/resources/role-die-cutting-medical-device-industry/