Thermal-Runaway Mitigation for EV Batteries: The Path to Safer Electric Mobility
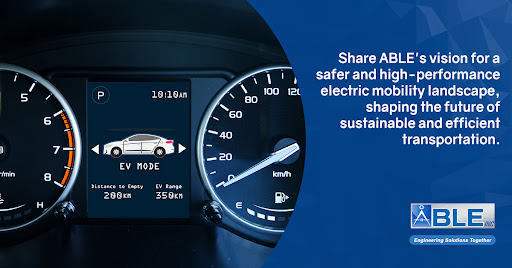
At ABLE, our seamless collaboration extends across various industries, with a strong focus on the automotive sector. Amidst this landscape, the electric vehicle (EV) segment stands out, demonstrating remarkable growth, particularly in the demand for vital components such as battery packs.
Within this burgeoning EV industry, a trajectory of expansion is foreseen for not only the coming decade but well into the future. This growth underscores an escalating requirement for EV batteries that are not only dependable and secure but also economically efficient. However, the integration of these battery packs into vehicle frameworks introduces fresh design complexities. A pivotal challenge revolves around the incorporation of functional materials—ones that avert thermal runaway—within the confined spaces characteristic of modern battery packs.
This predicament stands as a significant hurdle encountered by prominent players in the battery industry, including giants like Tesla, who are steadfastly engaged in refining and fortifying their solutions against this issue.
The forthcoming article delves into an ingenious remedy poised to tackle the thermal runaway concern head-on. The solution in question empowers engineers with a remarkable degree of adaptability in their endeavors with contemporary battery designs. This empowerment is made possible through the integration of pressure-sensitive adhesive tapes infused with cutting-edge functional materials.
EVs and EV Batteries: Assessing the Current Market and Future Outlook
According to Malcolm Gladwell’s definition, a tipping point is the critical mass, threshold, or boiling point. The International Energy Association predicts EV sales will surpass an 18% market share in 2023, a significant tipping point milestone. The growing adoption of EVs is driven by consumers’ changing preferences, environmental concerns, and governmental regulations in the EU, Asia, and some U.S. states. Consequently, owning and operating an internal combustion engine (ICE) vehicle may become challenging in these regions. Carmakers are responding to this shift by investing over $500 billion in EVs by 2030, with Tesla accounting for about a fifth of that commitment. Established OEMs like GM, Ford, Stellantis (formerly Fiat Chrysler Auto and PSA Group), Honda, and Volkswagen also make substantial investments.
The EV marketplace is projected to reach 25.5 million sales globally by 2030, a significant increase from the 2.3 million vehicles sold in 2020, representing a Compound Annual Growth Rate (CAGR) of 27%. Additionally, hybrid and plug-in hybrids are expected to account for another 21 million vehicle sales by the end of the decade.
By 2030, EVs, HEVs, and PHEVs will require 2 million MWh of battery power, a significant surge from less than 500,000 MWh in 2022, as reported by Avicenne. To meet this demand, global battery production capacity will grow from 450 GWh in 2020 to 2,800 GWhr in 2030. North America is expected to contribute 12% of this production by the end of the decade. As more OEMs establish goals and commitments for EV production and sales, EV vehicle designs are evolving beyond their ICE vehicle predecessors.
The Soaring Demand for EV Batteries: Impacts on Battery Pack Design
The EV market is experiencing rapid growth, but persistent engineering challenges still need to be addressed for widespread consumer and regulatory acceptance of EVs. Among these challenges, one of the most significant is fire and thermal-runaway mitigation. This affects various aspects of the EV battery industry, including shipping, charging, crash safety, and end-of-life considerations. China and the EU have taken the lead in establishing safety regulations for EV batteries, setting a standard for the rest of the world. A combination of different materials may be necessary across the industry to tackle this issue.
Thermal-runaway mitigation remains a major engineering hurdle in the development of EV battery packs. One potential solution involves integrating functional materials with pressure-sensitive adhesive tapes.
In the meantime, EV battery design is evolving towards structural packs in prismatic, cylindrical, and pouch-cell formats, which are integrated into the vehicle’s structure and are thinner than previous-generation packs. However, this reduced thickness leaves limited space for non-cell materials, including those needed for fireproofing and thermal-runaway mitigation. Despite claims that lithium iron phosphate (LFP) battery technology is safer, concerns about flammability persist.
For example, a notable incident in China in May 2021 involved an electric bus equipped with an LFP battery that caught fire during charging, subsequently spreading to and destroying four other buses. Luckily, there were no occupants in the buses, and no injuries were reported. As Original Equipment Manufacturers (OEMs) and their suppliers grapple with this challenge, materials featuring pressure-sensitive adhesive tapes for fireproofing and thermal-runaway mitigation present a potential solution.
A Closer Look at Pressure-Sensitive Adhesive Tapes
Pressure-sensitive adhesives create bonds with other materials through brief contact and light pressure. These adhesives come in various forms, such as label constructions and tapes. The adhesive is typically combined with a carrier material, like film, foam, or other substances in tape form. This carrier may also serve a functional purpose, such as being fire-retardant foam. Pressure-sensitive adhesive tapes find applications in diverse industries, including automotive, aerospace, building and construction, electronics, general industrial, and print and packaging. Moreover, they are utilized in various aspects of EV batteries, including thermal-runaway mitigation.
A pressure-sensitive adhesive establishes a bond when it comes into contact with a substrate, requiring only light pressure. This pressure initiates adhesive flow over the substrate and activates intermolecular forces like interlocking, chemical bonding, or Van der Waals forces. The adhesive’s viscosity allows elongation, absorbing energy and effectively holding the tape in place. Consequently, tapes offer several advantages over other securing methods, including lower tooling costs, no need for fasteners, uniform coverage, slim profiles, design flexibility, no curing or drying time, one- to two-year shelf life, and the ability to enable multi-layer functionality.
While there are numerous pressure-sensitive adhesive chemistries available, specific chemistries are better suited for EV battery applications than others.
EV battery tape constructions come in different forms: single-coated, double-coated, or transfer tape. Single-coated constructions have adhesive on one side of the carrier and are mainly employed for protective purposes. Double-coated versions have adhesive on both sides and are commonly used to bond materials together. On the other hand, transfer tapes deliver the adhesive directly to the substrate without needing a carrier. The choice of construction depends on the specific application within the battery pack.
The carrier film used in these tape constructions can offer additional benefits such as flame or dielectric protection. A typical tape construction comprises a release liner that safeguards the adhesive and film until the application process.
Enhancing Thermal-Runaway Prevention with Pressure-Sensitive Tapes
Thermal-runaway mitigation continues to be a pressing engineering challenge for EV batteries. Moreover, the shift towards a structural battery design reduces the available space between and around cells, making traditional fireproofing methods less effective. To address this issue, pressure-sensitive adhesive tapes integrated with functional fire prevention materials offer an efficient solution for thermal runaway mitigation within the battery pack. Utilizing inherently thin tapes integrated with functional fire protection materials proves effective in this context.
The specific applications and advantages of this approach include:
- Assembly Aid: Pressure-sensitive adhesive tapes are instrumental in securing thermal runaway materials during module assembly.
- Bonding: Double-coated tapes play a crucial role in bonding thermal runaway materials both to each other and within the battery pack’s structure. Moreover, they offer added design flexibility, facilitating the integration of functional materials even in narrow spaces.
- Material Protection: Single-coated pressure-sensitive adhesive tapes provide encapsulation and long-term protection for delicate, fibrous, flaky, and thermal runaway materials throughout the vehicle’s lifespan.
- Dielectric Strength: Pressure-sensitive adhesive tapes with dielectric films effectively prevent electrical arcing and short circuits.
Thermal-Runaway Mitigation Made Simple: Turnkey Solutions for EV Batteries
Functional materials integrated with pressure-sensitive adhesive tapes have the potential to revolutionize thermal-runaway mitigation in EV batteries. Given the rapidly evolving nature of this field, its significant role in collaborating with functional material manufacturers to assist OEMs and suppliers in developing practical thermal-runway solutions. Beyond our product portfolio, we offer extensive application and 3D design support and comprehensive testing capabilities. These include flame and dielectric performance, environmental factors, compression testing, battery cycling simulation, and bulk property testing (peel, tack, and shear). All testing is conducted in ISO-certified laboratories, ensuring high-quality results.
As the EV battery industry faces critical engineering challenges in the coming decade and beyond, thermal-runaway mitigation remains a key concern. Traditional fireproofing methods and materials may not be fully compatible with the evolving design of EV battery packs. However, functional materials integrated with pressure-sensitive adhesive tapes offer an easy-to-use, versatile, and effective solution, making them an ideal choice for many OEMs and suppliers.
Securing EV Battery Safety
Thermal-runaway mitigation remains a critical engineering challenge in the rapidly evolving landscape of EV batteries. As an industry leader, ABLE recognizes the paramount importance of addressing this concern. Integrating functional materials with pressure-sensitive adhesive tapes emerges as a game-changing solution. ABLE acknowledges its broader role in working with functional material manufacturers to assist OEMs and suppliers in devising effective thermal-runaway solutions.
Beyond providing a product portfolio, ABLE offers extensive application and 3D design support, along with comprehensive testing capabilities conducted in ISO-certified laboratories. This commitment ensures the development of efficient, safe, and reliable solutions, reinforcing the company’s dedication to advancing the safety and sustainability of EV battery systems for the future. With ABLE’s efforts, the outlook for thermal-runaway mitigation in EV batteries is set for transformative advancements, empowering the growth and success of electric mobility while prioritizing safety and environmental responsibility.
Are you interested in learning more about our automotive solutions? Contact ABLE today, and we’ll be more than happy to assist you!
References:
https://yoursolution.tapes.averydennison.com /acton/attachment/5107/f-fedfaf3b-47e1-4012-964f-e82cf06182c3/1/-/-/-/-/PTNA23%20Whitepaper%20Thermal%20Runaway%203May2023.pdf?utm_term=PTNA23%20Whitepaper%20Thermal%20Runaway%203May2023.pdf&utm_campaign=TEST-In%20depth%3A%20Mitigate%20thermal%20runaway%20in%20EV%20batteries&utm_content=email&utm_source=Act-On+Software&utm_medium=email&sid=TV2:OUpzS3oIV&sid=TV2:3iiJYTNYE
https://www.iea.org/ news/demand-for-electric-cars-is-booming-with-sales-expected-to-leap-35-this-year-after-a-record-breaking-2022#