The Difference Between Laser Cutting and Die Cutting
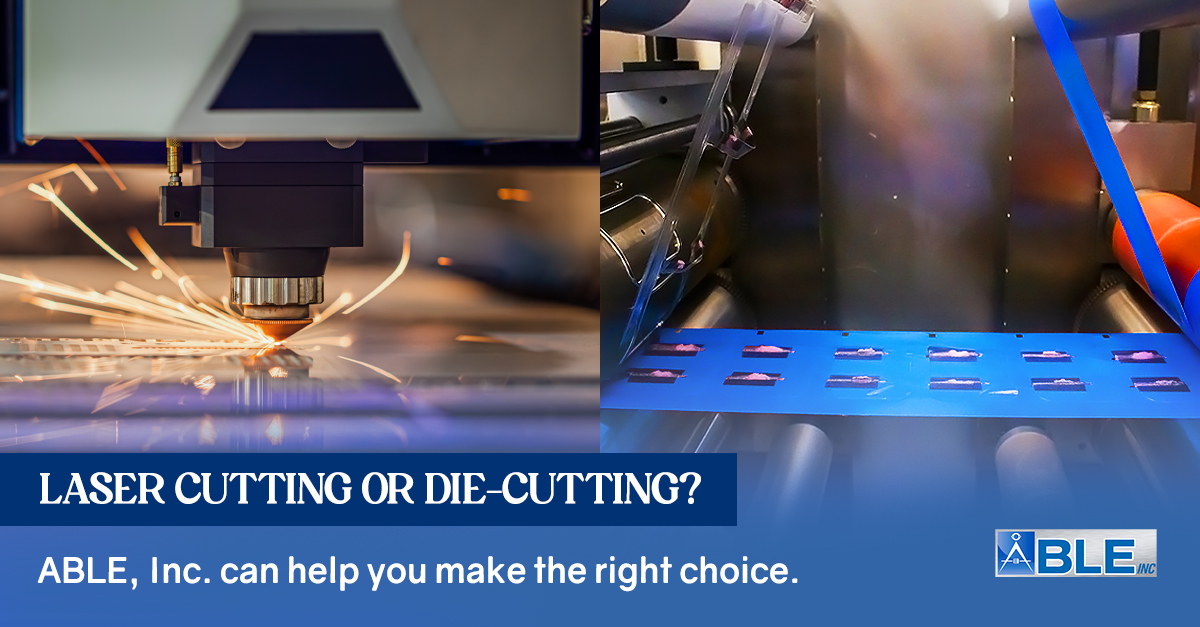
Many industries rely on precision cutting techniques as part of the manufacturing process. Two of the most common cutting methods are laser cutting and die cutting. While both methods provide a range of benefits, the right cutting technique for an individual application ultimately comes down to the requirements of the specific project. When comparing laser cutting and die cutting, considerations may include cost, volume, materials, and degree of precision. But first, let’s define these two cutting methods.
- Laser cutting is a cutting method that cuts materials into extremely precise shapes using a high-powered industrial laser. As the shape emerges, an assist gas blows away any melted material from the cut. Laser cutters operate through a series of instructions derived from a computer-aided design (CAD) file.
- Die-cutting is a cutting method that creates shapes out of softer, more flexible materials like plastic, foam, paper, cork, and others through cutting or perforating with a press. Die-cutting has a lot of methods including rotary, matched metal, and flatbed.
Benefits of Laser Cutting and Die Cutting
Now that you understand each cutting method’s basic mechanics, let’s dive into their benefits and limitations:
Benefits of Laser Cutting
Laser cutting has a broad usage across myriad industries, such as aerospace, automotive, electronics, medical, and many more. Some of the benefits offered by laser cutting processes include:
- Complex shapes can be laser cut from various mediums, such as fabrics, plastics, synthetics, woods, papers, and other organic materials.
- Laser cutting’s high level of accuracy helps to minimize waste during the cutting process.
- Extremely precise cutting, with an accuracy of +/- 0.1 mm.
- Due to extremely high precision, laser cutting generates virtually identical cuts throughout a production run.
- Laser cutting needs no time-consuming tool changes and accomplishes cutting operations quickly.
- The laser cutting process is also highly automated and requires little or no human intervention once programmed.
- This cutting method causes no distortion or warping even on thin materials due to the speed of the cut.
Benefits of Die Cutting
Die cutting is an ideal cutting method for high volumes, but not recommended for low-volume production or thicker materials. Several industries that implement the die-cutting method include aerospace, automotive, appliances, shipping, and medical devices, among others. Here are some of the advantages of die-cutting processes:
- Die cutting implements less material is wasted around the shapes than with other cutting methods.
- With only one machine needed, the die-cutting process is cost-effective and efficient in terms of how much time it takes.
- A die-cutting machine can fashion shapes with a single punch so that identical forms can be made quickly. A manual die cutter creates shapes more quickly than any cutting method.
- Industries can achieve pretty complex shapes, with multiple cuts and multiple layers.
- Die cutting allows for creating shapes that look terrific, and for creases in cards and plastic.
Limitations of Laser Cutting and Die Cutting
Die-cutting and laser processes have some limitations as well. Several industries must identify these disadvantages so that they can pick the right cutting method for their needs.
Limitations of Laser Cutting
Although laser cutting is used to produce parts in almost every industry, this cutting method does have downsides.
- Energy consumption is not fixed. It is dependent on the amount or piece that you want to cut.
- While human involvement is not much needed in laser cutting, humans are needed for repairs or inspection of laser machines.
- Production rate may change depending on the type of material and the thickness of the sheet.
- Some metals like copper and aluminum are difficult to cut in the laser machine.
- Improper settings of the laser-cutting machine can cause burns.
- Laser cutting is a bit expensive when compared with other techniques of cutting sheets.
Limitations of Die Cutting
Die cutting has some potential drawbacks which everyone needs to know.
- Because the cutting tool incorporates a sharp blade, die cutting can be dangerous unless the person completing the task knows what they are doing.
- Industries need a new die for each design they create.
- It is less cost-effective if companies are not using this technique that often and only need low volume.
- It may not be the cutting method of choice if companies are working with thicker materials.
- Length, height, and width are subject to the limitations of the rotary die-cutting machine, so if companies want large-format printing such as office signage or retail branding, it may not be the right choice.
CNC Machining
In addition to laser cutting and die cutting, another essential cutting technique that plays a pivotal role in precision manufacturing is CNC machining service. CNC, or Computer Numerical Control, machining involves using automated tools to remove material from a workpiece, resulting in highly accurate and intricate shapes. This method is widely employed across various industries and can be a crucial consideration when evaluating cutting techniques for specific projects.
Benefits of CNC Machining
CNC machining offers distinct advantages that make it a preferred choice in certain applications. Some key benefits of CNC machining include:
- Versatility: CNC machining can be applied to a wide range of materials, including metals, plastics, and composites, providing versatility in manufacturing.
- High Precision: Similar to laser cutting, CNC machining delivers exceptional precision with tolerances as tight as +/- 0.1 mm, ensuring consistency throughout production.
- Material Compatibility: CNC machining is well-suited for working with challenging materials like metals, including copper and aluminum, overcoming some of the limitations faced by laser cutting.
- Automated and Efficient: The CNC machining process is highly automated, minimizing the need for constant human intervention and facilitating efficient production runs.
- Complex Shapes: It allows for the creation of intricate and complex shapes, making it suitable for a variety of industries, including aerospace, automotive, and electronics.
Which Is Better?
Choosing a cutting method depends on your project, so it isn’t a case of laser cutting vs. die cutting, or which one is best, but which cutting method best suits what you’re aiming to achieve. It’s essential to clearly define your project goals and budgets from the onset to help you make the right choice. If you want our help, ABLE can guide you on the right cutting method to use in your projects. So, what are you waiting for? Talk to us now!